How Rotomolding Delivers Strength, Durability, and Design Flexibility
How Rotomolding Delivers Strength, Durability, and Design Flexibility
Blog Article
Rotational molding, frequently called Plastics Rotomolding, is a vital approach in industrial plastic manufacturing, enjoying a substantial role in producing durable, high-quality products and services across various industries. That production strategy has been embraced because of its power to produce delicate, worthless plastic things that are both strong and lightweight, rendering it a go-to method for a wide range of commercial applications.
What Makes Rotational Molding Therefore Important?
Rotational molding presents unique benefits over different plastic production processes. Unlike procedure molding or hit molding, rotomolding requires heating plastic resin inside a form, while turning it along numerous axes. This process effects in a level finish of plastic on the interior surface of the shape, permitting uniform depth and an easy finish.

This original method is very valuable in industries where durability, strength, and opposition to use and grab are crucial. Rotational molding is ideal for providing big, hollow pieces such as for instance storage tanks, bins, and containers, as well as smaller things like automotive components and underwater products. Their capacity to create seamless, sturdy products with high influence weight assures that these materials may resist harsh surroundings, creating them crucial in industries like agriculture, structure, and logistics.
Crucial Benefits of Rotational Molding
Among the standout benefits of rotational molding is its flexibility in design. The process can accommodate complicated forms and various wall thicknesses, allowing producers to meet up specific design specifications. Furthermore, the lack of stitches or weld lines promotes the strength and endurance of the merchandise, eliminating possible weak areas that can lead to failure under stress.
Rotational molding also helps the utilization of a wide selection of components, giving companies more possibilities in regards to choosing the proper plastic due to their needs. Whether it's a very durable substance for heavy-duty purposes or even a light option for client goods, the versatility of this method assists cater to varied production needs.
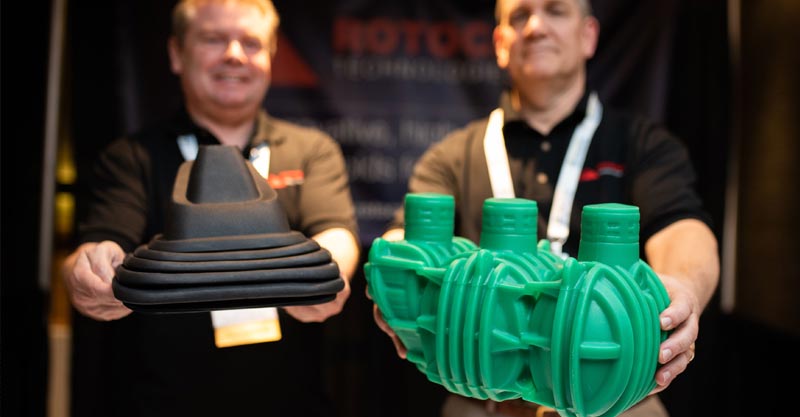
Sustainability and Cost-Effectiveness
Another key gain may be the sustainability aspect of rotomolding. The process generates small waste since surplus material can often be recycled and recycled in potential creation runs. Furthermore, the energy-efficient character of rotational molding makes it a cost-effective choice for large-scale creation, enabling organizations to maintain competitive pricing while however achieving supreme quality results.
Conclusion
Rotational molding is a cornerstone of commercial plastic manufacturing, giving advantages that go much beyond simple manufacturing. Their ability to create resilient, variable, and cost-effective plastic products and services with small spend makes it an essential method for many industries. As professional needs continue to grow, the importance of rotational molding in offering trusted, sustainable solutions will only increase, solidifying its place as an integral technique in modern manufacturing. Report this page