Why Rotational Molding is Ideal for Large, Hollow Plastic Parts
Why Rotational Molding is Ideal for Large, Hollow Plastic Parts
Blog Article
Rotomolding, also referred to as rotational molding, can be an revolutionary manufacturing process that provides a highly cost-effective solution for making supreme quality plastic products. This versatile process has acquired significant popularity in recent years due to its capacity to produce resilient, light, and delicately developed plastic items. Whether for industrial, industrial, or client use, Rotational Molding is just a chosen choice for many industries looking for trusted and inexpensive manufacturing solutions.
How Rotomolding Operates
The method of rotomolding requires the use of a mold that is rotated on numerous axes while plastic dust or resin is heated in the mold. Since the substance is heated and dissolved, it evenly coats the interior areas of the mold. The shape is then cooled, solidifying the plastic in to its final shape. This excellent process makes for the creation of hollow pieces, complicated shapes, and uniform thicknesses that might be hard or impossible to accomplish with other molding techniques.

Critical Benefits of Rotomolding
Cost-Effective Manufacturing: Rotomolding is one of the very most affordable plastic production methods, specially when producing moderate to big quantities. The conforms found in rotomolding are generally less expensive than shot molds or blow shapes, which makes it an attractive option for companies seeking to help keep charges low.
Versatility in Style: This process enables manufacturers to produce a wide variety of styles, styles, and patterns, rendering it perfect for programs that need custom or unique products. The flexibleness in style also assures that companies can generate products and services with different wall thicknesses, which plays a role in the toughness and functionality of the finished product.
Toughness and Power: The plastic pieces developed through rotomolding are noted for their power and resistance to influence, creating them ideal for outdoor and heavy-duty applications. Also, the method assures even circulation of product, which effects in products with standard width and improved durability.
Environmental Sustainability: Rotomolding is also an green process. As it employs relatively reduced amounts of energy and produces small spend, it can help minimize the environmental presence associated with manufacturing. Several companies are now prioritizing eco-friendly production techniques, and rotomolding fits effortlessly into these sustainability goals.
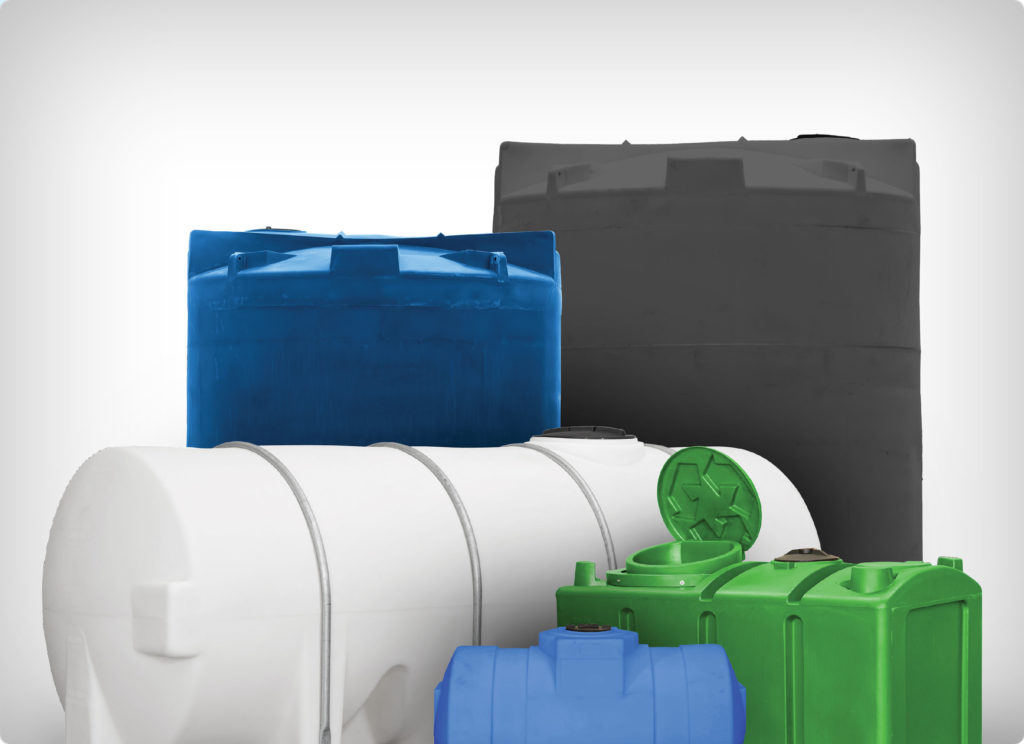
Purposes of Rotomolding
Rotomolding is found in a wide range of industries, from automotive to agriculture, and even toys and recreational products. It's frequently applied to generate large things such as for example storage tanks, watercraft, and playground equipment, along with smaller, intricate components like components for medical devices. The versatility of rotomolding helps it be a go-to alternative for industries looking to innovate with plastic products.
Conclusion
Rotomolding offers an successful, cost-effective, and versatile technique for producing high-quality plastic products. Using its capacity to produce complicated patterns, toughness, and minimal creation fees, it's no surprise that therefore several industries are turning to this method due to their manufacturing needs. As need for high-performance plastic products keeps growing, rotomolding is defined to enjoy an increasingly essential position in surrounding the future of plastic manufacturing.
Report this page